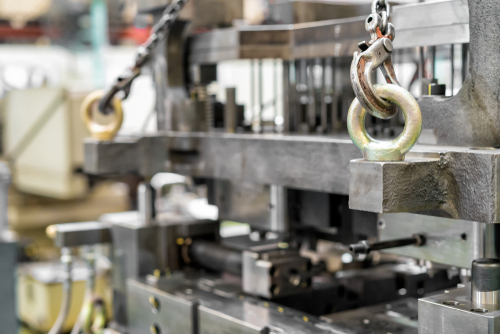
We have covered a few of the most common plastic manufacturing processes including processes like thermoforming. Every process has different pros and cons, and as a company you need to decide which system is best for your needs. Generally speaking, many of the pros and cons come down to cost vs quality and consistency over time. Today we will look at how aluminum die casting compares to injection molding in regards to pricing and materials used.
What Is Aluminum Die Casting
Similar to injection molding, aluminum die casting starts with similar steps. Aluminum die casting involves creating an aluminum die in the form of the part you plan to create. Metal is then liquified and using extreme pressure it is injected into the die. The die is then cooled and the die is opened to reveal the finished product. The key difference between aluminum die casting and plastic injection molding is the material used. Aluminum die casting creates metal products whereas injection molding creates plastic products.
Pros And Cons Of Using Aluminum Die Casting
Aluminum die casting provides metal components that have some benefits over plastic components created through injection molding. Aluminum die casting can create metal parts efficiently and to a high degree of accuracy. Also in some cases, metal has a high tolerance and greater durability than plastic pieces. However, the materials are much more expensive as well as labor costs. Over time those costs will add up with each run of the product. Metal pieces are good when absolutely needed and for smaller and shorter runs.
Pros and Cons of Using Injection Molding
We have spoken at length on how injection molding provides value to manufacturers. Generally, injection molding allows for the consistent mass production of a plastic piece. By using metal molds, intricately designed pieces with complex geometry can be mass-produced again and again with little to no mistakes. Plastic resin is inexpensive compared to its metal counterparts and parts can be made quickly. As for durabilities, fillers can be used in plastic molds to increase the strength of the final product. Plastic is also a more flexible material, both in its pliability and also the variety of advantages it can give a manufacturer. Plastic pieces can be fine-tuned based on specifications need for strength, durability, bend-ability, and other factors whereas metal cannot. Plastic production is also quicker than metal production and plastics do not rust or corrode. However, in certain circumstances, metal components are needed and aluminum die casting is the better option.
Plastic Injection Molding in Massachusetts
Learn more about plastic injection molding and the best manufacturing process for plastic parts from Lee Plastics Inc. in Massachusetts. Our team would be happy to answer any of your questions on manufacturing plastic components or make a bid on your manufacturing project. Give us a call or contact us online to learn more.